Distillery Effluent
ETP SYSTEM FOR MOLASSES BASED DISTILLERIES
Distilleries have been generating huge quantities of high toxic effluents and in spite of the best efforts made so far a comprehensive treatment has not been possible. In most of the conventional technologies, the treated effluent also yields very high BOD, COD, TS and TDS level with black colored and odor effluent to rivers & natural water streams. Based on the above mentioned fact, a treatment by which it will be possible to overcome all the problems have been worked out. The basic thrust of the technology is to reduce the quantity by a maximum possible extent. The concept and the treatment is based on the belief that the entire BOD requirement should go down and the condensate coming out should not be polluted.
KEY FEATURES OF MULTI EFFECT EVAPORATOR SYSTEM:
- Fully Customized Designed System Highest Steam Economy
- Lowest Operation & Maintenance Cost
- Operator Friendly
- Easily Upgradeable
- Generation of Reusable Condensate Water
FLOW DIAGRAM OF MULTI EFFECT EVAPORATION SYSTEM
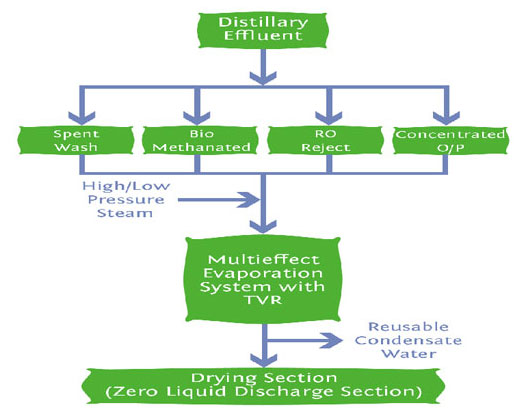
ZERO LIQUID DISCHARGE SECTION (FLOW)
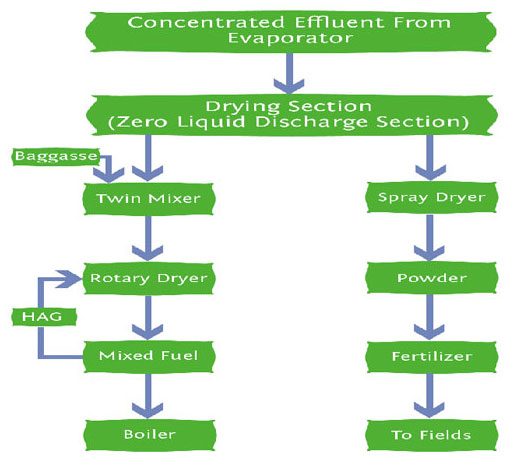
DISTILLERY WASTE WATER HANDLING BY EVAPORATION AND DRYING
The technology is based on basic principle of reduction of quantity by concentrating the effluent and subsequently drying it to a Powder / Mixed Fuel form which can be used as an alternative fuel for boilers and as an organic / inorganic fertilizer for plant growth.
THE EVAPORATION PROCESS:
Distillery Effluent is fed to the vacuum evaporator to concentrate maximum up to 60% solids concentration. The total process is under vacuum and the vapors generated in the system are re-used to economize steam consumption. In order to reduce steam consumption in multiple effect evaporation system the thermal vapour recompression system is used. The thermal vapour recompression system use Vapours generated in the evaporator and compress it by steam and the compressed vapours are used as heating medium in the evaporator. Water recovered from the evaporator has low BOD value and can be recycled in the plant.
THE DRYING PROCESS (ZERO LIQUID DISCHARGE SECTION):
The resultant slurry (concentrate) is fed to the drying section for converting the liquid concentrate to powder / mixed fuel (mixing with Secondary Fuel e.g. Bagasse, rice husk etc.) form. The air heated by steam radiator or hot air generator is fed into the dryer. The whole system is designed to obtain the optimum results. The emissions from the dryer are within the norms specified by the Govt. of India. This powder / mixed fuel can be used as an alternative fuel to steam boilers.
MAIN THRUST OF THE TECHNOLOGY
The Basic thrust of the technology is to reduce the quantity of Effluent by a maximum possible extent in the first stage.
In many of this kind of processes foaming is a big problem, which carries away lot of suspended particles in the condensate water, which eventually increases the BOD of distillate. The SSP’s technology has taken care of this problem and the BOD levels are contained to an extent of 80 mg/l and the distillate produced is colorless and is reusable for other processes.
KEY FEATURES (GENERAL):
- ZERO Liquid Discharge
- Low Operating Cost
- User Friendly
- Easily Upgradeable
- Less Downtime for Maintenance
- Applicable for CDM Benefit